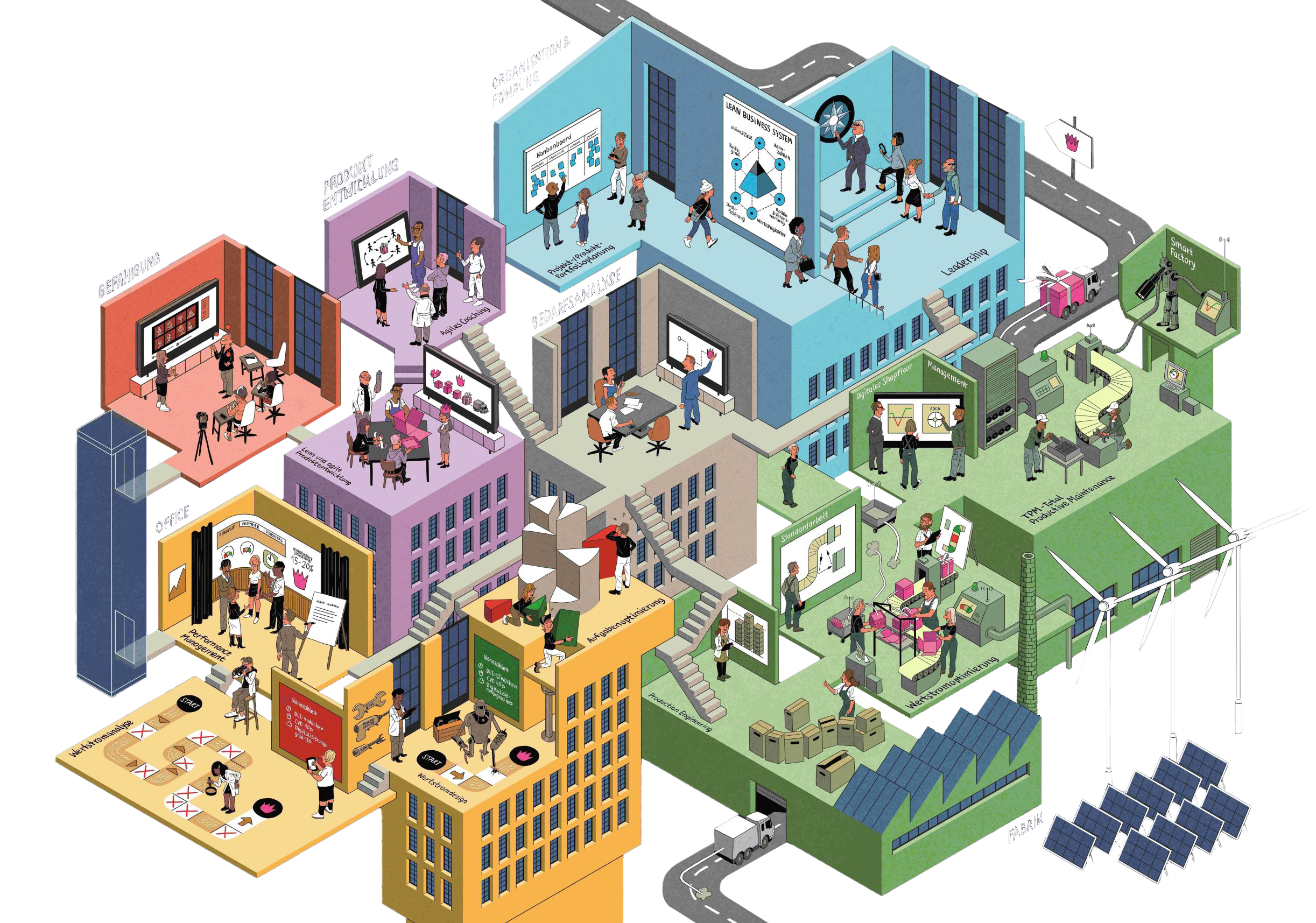
Sector / division: Utilities industry / administration
Project focus and goal: Qualification and coaching of lean senior experts, implementation of lighthouse projects, development of lean rollout concept
Approach, tools and methods:
- Qualification of Lean Senior Experts in trainings lasting several days
- Management workshop with elaboration of why and wherefore
- Methods used: Customer Journey, SIPOC, value stream analysis, activity structure analysis, capacity calculation, visual management, Kanban Board, retrospective
Results:
- Target processes developed to enable growth of the business unit
- Lean management convinced and rollout concept developed
- Transfer of Lean activities to the technical areas started
Would you like to learn more? Contact Judith Fellsches
Industry / Division: Plant Engineering / Sales, Offer Management, Engineering, Supply Chain, Manufacturing, Order Execution
Project focus and goal: Analysis, conception and implementation; development of dashboard for OFM, process optimisation and subsequent digitalisation and automation
Approach, tools and methods:
- Potential analysis via order execution, prioritisation of implementation topics with plant management
- Development of OFM, optimisation of interface
- Methods used: E2E value stream, KPI, visual management, dashboard with Tableau, Analytic Process Automation with Alteryx, process design, digitalisation and automation of the quotation process, Kanban Board
Results:
- Officefloor: a dashboard shows the OTD and DLZ for the overall process and for the respective process sections and officefloor meetings take place. Transparency for the PDCA has been created.
- Optimization interface: A workflow that simplifies and controls the process has been implemented. Defined "rules of the game" are measured via the process. Transparency for all participants is increased, responsibilities are clearly defined and the process is simplified by the workflow.
Would you like to learn more? Contact Judith Fellsches
Sector / division: Utilities industry / various locations, assembly/production, service
Project focus and goal: Implementation of Lean principles and methods in production areas
Approach, tools and methods:
- One-week power workshops incl. as-is analysis, conception and implementation with those involved in the respective production areas (e.g. assembly, repair, complaint processing)
- Tools used: Lean Production, Value Stream Mapping, Takt Time Diagram, Card-Board Engineering, Visual Management, Shopfloor Management, Spagetti Diagram, 5S, Standardisation, Segmentation, Capacity Analysis, Qualification Matrix.
Results:
- Enthusiasm of managers and employees
- Implementation of Lean principles in selected production areas
- Significant improvements in productivity, delivery reliability, lead times and quality
- Sustainable establishment of an improvement culture based on the lean management philosophy
Would you like to learn more? Contact Ralf Langmaack
Industry / Division: Automotive / Production
Project focus and goal: Lean production, output increase on a line with unchanged employee deployment to meet OEM requirements
Approach, tools and methods:
- One-week analysis phase on site at the line, implementation of one-week power workshops, final effectiveness test in ongoing operations over one week
- Methods used: shop floor management, takt time diagram, Gemba, waste walks, chalk circle, balancing, standard work, visual management, KPI, layout, role definition (team leader, line leader, etc.), value stream mapping
Results:
- Full compliance with OEM requirements in terms of on-time delivery of the required target quantities of all variants.
- Sustainable output increase of 62% with the same number of employees
Would you like to learn more? Contact Ralf Langmaack
Sector / company division: Service industry
Project focus and goal: Lean administration, enabling employees in the pilot areas to apply Lean principles and methods in their everyday work and to optimise their own processes
Approach, tools and methods:
- Management Awareness Workshop to define the objectives and framework conditions
- Selection of two pilot areas according to pre-defined criteria
- Management training
- Awareness session for the pilot teams
- Process- and team-oriented Lean Admin rollout in the pilot teams
- Development of a rollout concept
- Methods and tools: Training, facilitation, potential analysis, self-organisation, value stream mapping, standardisation, team boards, office floor management, goal derivation for teams, leadership, change management, project management, agile ways of working, coaching
Results:
- Employees in the two pilot areas enthusiastic about the subject of Lean
- > 25% improvement potential identified
Would you like to learn more? Contact Judith Fellsches
Industry / Division: Utilities / all business units
Project focus and goal: Lean Administration, Hoshin Kanri, introduction of X-Matrix down to department level
Approach, tools and methods:
- Workshop with business unit managers to clarify expectations and tasks
- Presentation of Hoshin Kanri and X-Matrix
- Embedding the X-Matrix in the existing goal derivation and management process
- Development of the X-Matrices in workshops with stakeholders
- Tools: Hoshin Kanri, X-Matrix, facilitation, workshop, visualisation.
Results:
- Consistency of the focused goals is ensured through the procedure and use of the X-Matrix.
- For each business area, an X-Matrix was developed with the respective business area manager and department heads. For individual departments, an X-matrix was created on the third level.
Would you like to learn more? Contact Judith Fellsches
Sector / company division: Public company / administration, all areas
Project focus and objective: Design and delivery of training (basic and expert level), coaching as part of Lean projects
Approach, tools and methods:
- Conception of trainings
- Implementation of training on site and remotely
- Coaching in the group and individually for the implementation of the practical project
- Methods used: Training (Lean Admin Tools, Moderation, Presentation, Change), Coaching
Results:
- Qualification of Lean experts incl. implementation of practical projects
Would you like to learn more? Contact Judith Fellsches
Industry / Division: Automotive
Project focus and goal: Agile development organisation, establishment of a common agile understanding and agile working methods
Approach, tools and methods:
- Support in the establishment and staffing of the Scrum teams, methodical coaching of the Scrum teams & situational training
- Scaling and synchronisation of the agile teams within the overall organisation
- Planning and implementation of internal agile events as part of the transition, e.g. Big Room Planning
- Regular maturity measurement for a structured empowerment of the agile teams
Results:
- Teams can competently apply the agile process, internal role holders can take responsibility independently
- Continuous realistic agile planning of the new IT solution
- Higher-level synchronised release planning between the agile and non-agile teams
- Experience with agile techniques at the level of the overall organisation
Would you like to learn more? Contact Christian Jagla
Sector / company division: IT department, demand management.
Project focus and objective: Workshop with demand managers to define improvement measures to increase the quality of IT demands. For this purpose, the relevance of acceptance criteria is presented and tested.
Approach, tools and methods:
- Conception and implementation of a one-day workshop
- Contents: Why acceptance criteria, explanation of acceptance criteria based on real examples, exercise on defining acceptance criteria, reflection on experiences gained.
Results:
- Enabling the demand managers to use acceptance criteria.
- Selection and commitment to three measures that are implemented in everyday life
Would you like to learn more? Contact Judith Fellsches